The most important function of packaging is to protect the quality of all packaged goods, that is, to ensure that the goods will not be damaged, lost, leaked and spoiled.
This requires that the seal must have a certain strength and sealing performance in the process of bag making, and can withstand the pressure of a certain weight of content to ensure that the product does not crack or leak during the circulation process, so as to achieve the purpose of protecting the product. And bag making is the last production process before delivery to users, and quality control is more important.
Material selection
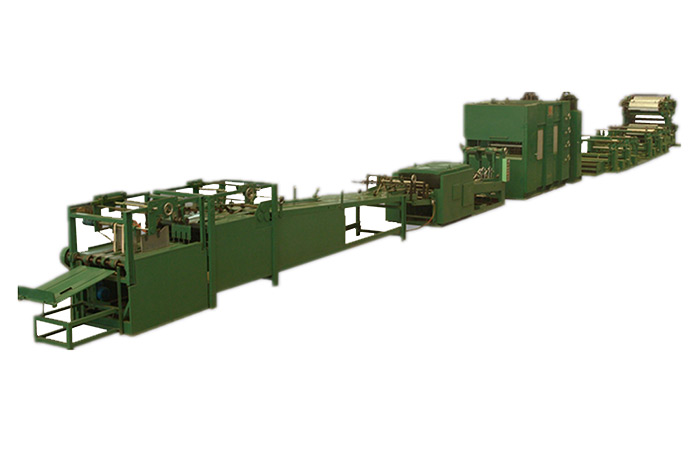
Surface material
Most of the non-heat-sealable materials are used, and materials with good heat resistance and small thermal deformation should be considered, such as BOPA, BOPET, BOPP, paper, etc.
Inner material
That is, the heat-sealable material can be heat-sealed at a temperature 30°C lower than the heat-deformation temperature of the surface-layer material. If the temperature is low, the sealing fastness is poor and cannot meet the requirements. In order to improve the sealing fastness, the temperature is raised. Because the thermal deformation temperature difference between the inner and outer layers is too small, the surface material is easily scalded.
For the same heat-sealing material, its heat-sealing strength will increase as the thickness of the heat-sealing material increases. Therefore, the inner layer material of the back sealing bag and the stand-up bag should be more than 30μm thick. If the inner layer material is too thin, it will affect the sealing of the finished bag.
Zipper
A zipper seal with a lower heat-sealing temperature should be used, generally 5~10°C lower than the heat-sealing temperature of the inner layer material, such as the PE L-101 zipper seal of Zhongshan Zhongcheng Packaging Materials Co., Ltd. Its PE LL-201 is about 10 ℃ lower, which can be selected when making bags with different PE inner layer materials, so as to achieve the best state of heat sealing with the inner layer material.
Preparation before bag making
1. Ensure that the composite layer of the composite film is completely cured, otherwise it will easily cause the deformation of the heat-sealed edge after bag making, which will affect the appearance of the bag;
2. Select an appropriate heat seal according to the requirements, and clean it up to ensure that the heat seal knife surface is flat, and check whether the heat insulation cloth is intact and flat;
3. Check the status of each part of the bag making machine, pre-set the pressure-sealing temperature according to experience (refer to the previous production conditions of similar materials), preheat, and start the formal production after reaching the preset temperature for 20 minutes. It should be noted that reaching the preset temperature does not mean that the heat seal has reached the preset temperature, and there needs to be a process of heat conduction to achieve equilibrium;
4. Adjustment of bag making process conditions Temperature, pressure and time (speed) are the three indispensable elements of heat sealing and the most important conditions for process parameters. Temperature, pressure and time (speed) need to be adjusted according to each other to achieve the best state.
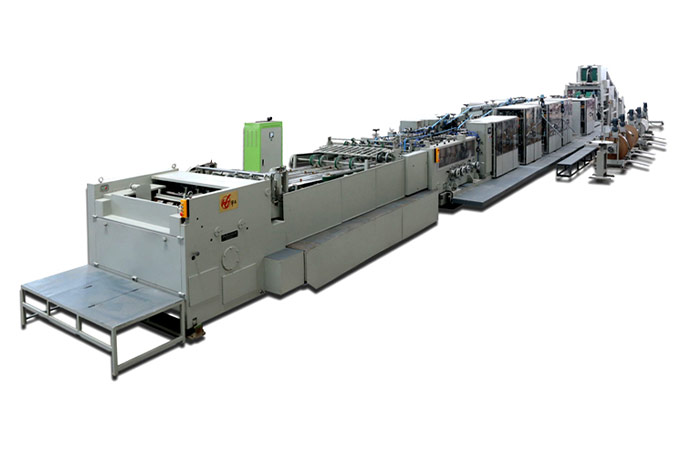
Heat sealing temperature
The heat sealing temperature has the most direct influence on the heat sealing strength, and it is the main basis for selecting the optimal viscous flow temperature state. The heat sealing temperature should be set according to the material, thickness and processing speed of the composite material. In the actual production process, due to the influence of various factors such as heat sealing pressure, bag making speed and the thickness of the composite substrate, the heat sealing temperature is often higher than the melting temperature of the heat sealing material.
If the heat sealing temperature is lower than the melting temperature of the heat sealing material, even if the pressure is increased and the heat sealing time is prolonged, the heat sealing layer cannot be truly sealed; if the heat sealing temperature is too high, it is easy to damage the heat sealing material at the seal. Greatly reduces the sealing strength.
Sealing pressure
Under normal circumstances, pressure is the first parameter to be adjusted and determined. Generally, there is no pressure indication in the equipment. It is suitable for the pressure end of the heat sealing knife to be about 3mm. The pressure balance (left and right or front and rear) is very important. It is difficult for the heat cover to be truly fused together, resulting in poor local heat sealing, and sometimes the phenomenon that the air bubbles caught in the welding seam cannot be removed cleanly.
If the compression is too large, the pressure will be too high, which will cause the heat sealing and the traction to be out of sync, and when the heat sealing temperature is high, the material at the sealing will be in a semi-molten state. If the pressure is too high, it is easy to squeeze out part of the heat sealing material. , so that the edge of the seal is in a half-cut state, causing the material at the seal to become thinner and brittle, and the heat sealing strength is reduced.
Sealing time (speed)
The sealing time not only affects the heat sealing strength but also the appearance flatness of the composite packaging bag. When the heat-sealing temperature and heat-sealing pressure are fixed, the longer the heat-sealing time is, the more fully the heat-sealing layer is fused, the stronger the bond, and the higher the sealing strength. Wrinkling affects the appearance smoothness.
Cool down
The cooling process is to use a lower temperature to shape the weld just after melting and heat sealing. The cooling temperature should be the lowest temperature at which the cooling knife does not accumulate condensed water. The cooling water should be circulated smoothly. If there is no condition to use the cooling water, the water flow should be increased as much as possible to ensure the cooling effect. If the cooling of the sealing edge after heat sealing is not enough, resulting in insufficient shaping, the internal stress cannot be eliminated, and the heat sealing strength and appearance will be affected.
Heat sealing times
The more times of heat sealing, the higher the strength of heat sealing. Generally, the number of times of heat sealing is required to be at least two times. The number of longitudinal heat sealing depends on the ratio of the effective length of the longitudinal heat sealing knife to the bag length; the number of transverse heat sealing is determined by the number of sets of transverse heat sealing devices in the bag making machine.
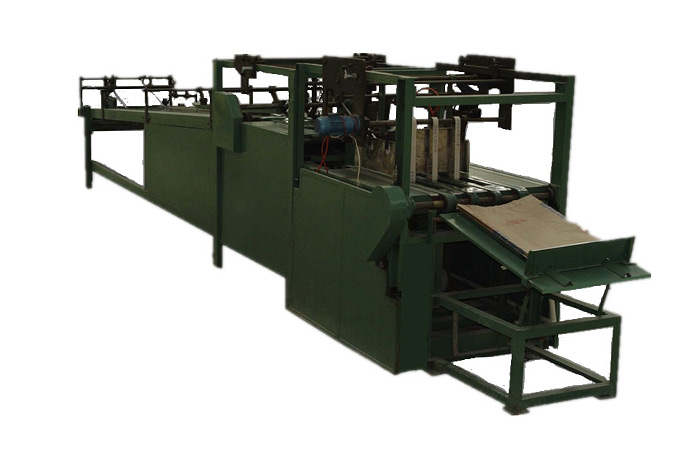
Process control
In the production process, the quality of the finished product should be continuously checked. In addition to the size and appearance visual inspection, the sealing strength and sealing performance should also be checked. Find problems and adjust them in a timely manner, and make detailed records. Taking the production of three-side sealing zipper bags as an example, the following items should be checked:
1. Heat sealing strength;
2. The size, flatness, appearance quality of the bag, front and rear alignment of the bag and other requirements of the customer, such as the position of the tearing opening, etc.;
3. The internal and external opening force of the zipper, the internal opening force of the PE zipper is generally required to be ≥50N/50mm, and the internal opening force of the PP zipper is generally required to be ≥60N/50mm. The PE LL-201 of Zhongshan Zhongcheng Packaging Materials Co., Ltd. can reach ≥ 70 N/50mm, PE Q501 can reach ≥80 N/50mm, the external opening force has different requirements according to the customer’s usage habits;
4. The sealing performance of the bag can be tested by spraying a dye-added penetrant into the seal to see whether it penetrates or not, or by filling the bag with water and hanging it upside down for 24 hours to see whether it seeps.
5. The flatness of the bag zipper. Heat sealing bag making is a heat transfer process, and its process is relatively uncomplicated, but there are many factors that affect its quality.
In addition to some of the above points, the peel strength of the composite film, the heat resistance of the printing ink, the precipitation of additives in the heat-sealing layer, the width of the heat-sealed edge, and the thickness uniformity of the composite film are all related to the final quality of the composite film bag. Comprehensive consideration should be taken in the production process.